Maximize Productivity with Automatic Label Applicators
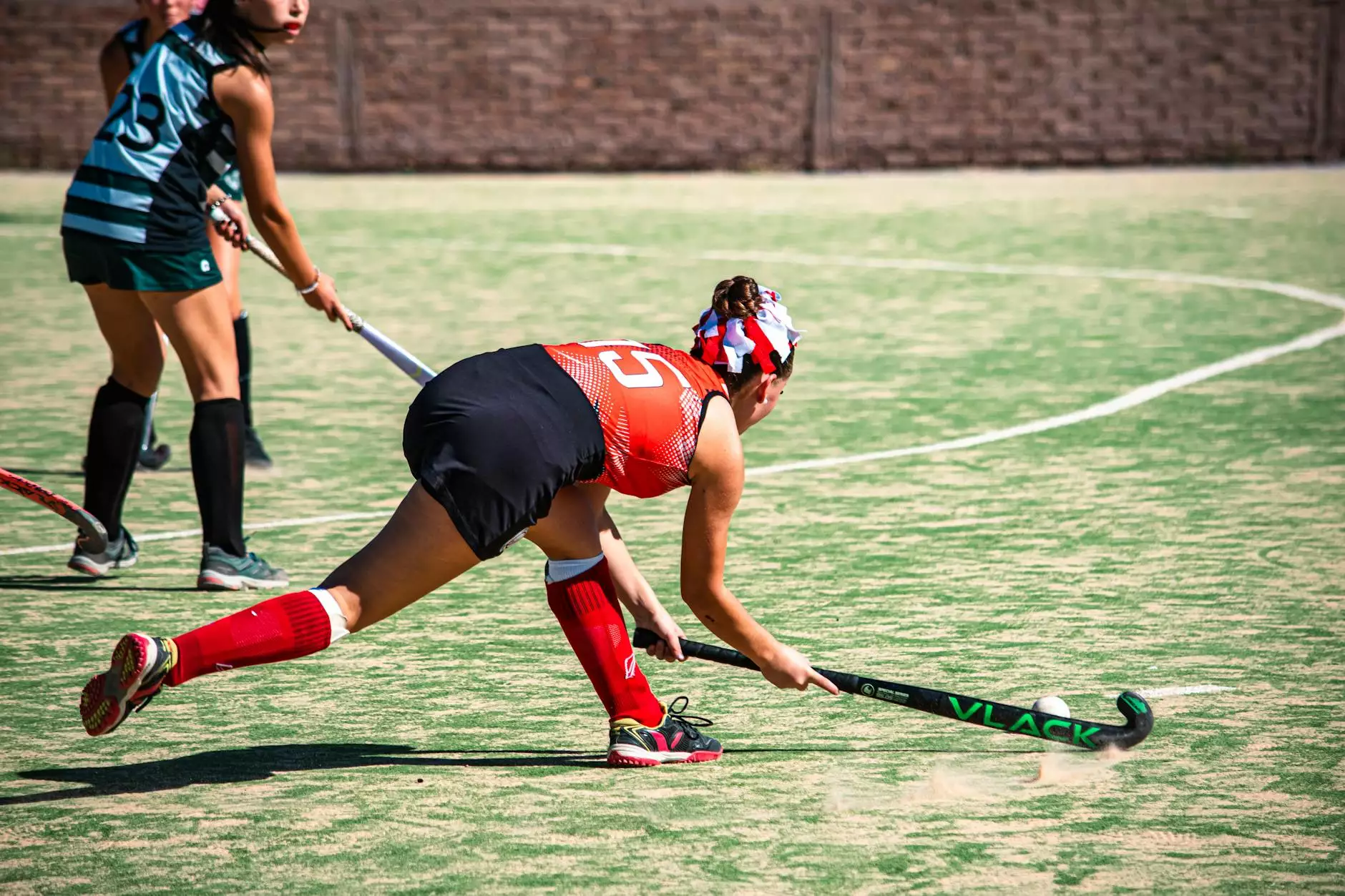
Automatic label applicators are transforming the landscape of labeling solutions across various industries. As a key component of the packaging and production process, these devices enhance efficiency, reduce labor costs, and ensure accuracy in label placement. In this comprehensive article, we will delve into the intricacies of automatic label applicators, their working mechanisms, advantages, and the factors to consider when choosing the right applicator for your business needs.
What are Automatic Label Applicators?
Automatic label applicators are specialized devices designed to apply labels to products, packaging, or pallets automatically. These machines can handle a variety of label sizes, shapes, and materials, making them versatile tools in industrial settings. By automating the labeling process, businesses can streamline their operations, minimize human error, and enhance overall productivity.
How Do Automatic Label Applicators Work?
The operation of automatic label applicators is straightforward yet sophisticated. Below is a detailed rundown of how these machines function:
- Label Feed Mechanism: Automatic label applicators utilize a roll of labels that feed into the machine. Sensors detect the presence of the labels and ensure a continuous flow.
- Label Separation: Once a label reaches the applicator, it is separated from the backing material using mechanical or pneumatic methods.
- Application Method: The applicator uses various methods, such as tamp or wipe-on, to apply the label onto the designated surface accurately.
- Quality Control: Most modern systems are equipped with vision systems to ensure that labels are correctly placed and free from defects, thereby maintaining quality standards.
Benefits of Using Automatic Label Applicators
The adoption of automatic label applicators can lead to a myriad of benefits for businesses, particularly in the realms of efficiency, accuracy, and cost-saving. Here are some of the key advantages:
1. Enhanced Efficiency
By automating the labeling process, businesses can significantly increase their output. These machines work faster than manual labeling methods, allowing for a higher volume of products to be labeled in a shorter timeframe.
2. Cost Reduction
Labor costs can escalate quickly, especially in high-volume production settings. Using automatic label applicators reduces the manpower needed for labeling tasks, which translates into significant cost savings.
3. Improved Accuracy
Human error is a common challenge in manual labeling processes. Automatic applicators ensure that labels are applied consistently and accurately every time, reducing waste and rework.
4. Versatility
These devices can cater to various labeling needs — whether it's for bottles, boxes, or pallets. This flexibility makes them suitable for a wide range of industries, including food and beverage, pharmaceuticals, and electronics.
5. Better Quality Control
Automatic label applicators often come equipped with advanced technology that includes inspection systems. These systems detect misapplied or missing labels, ensuring only products that meet quality standards reach the market.
Types of Automatic Label Applicators
There are various types of automatic label applicators, each designed to meet differing operational needs. Here are some common types:
- Top Labeling Machines: These machines apply labels on the top surface of products, perfect for items like box tops and jars.
- Side Labeling Machines: Ideal for labeling the sides of products, these machines are commonly used for bottles and containers.
- Wrap-Around Labeling Machines: These are used for cylindrical products where labels are wrapped around the entire item, such as beverage bottles.
- Rotary Labeling Machines: Suitable for high-speed operations, these machines apply labels to products in a continuous fashion.
Choosing the Right Automatic Label Applicator
Selecting the correct automatic label applicator requires careful consideration of multiple factors. Here are some critical aspects to assess:
1. Product Specifications
Understand the dimensions, shape, and material of the products you will be labeling. Different automatic label applicators are optimized for different types of products.
2. Label Size and Type
Consider the size and materials of the labels you plan to use. Some applicators are specialized for certain label materials, like paper or plastic, and dimensions.
3. Speed and Volume
Evaluate your production speed requirements. Choose an applicator that can handle your expected volume without sacrificing label application quality.
4. Integration with Existing Systems
Ensure that the label applicator can integrate smoothly with your existing production line and packaging machinery for efficient operation.
5. Budget
While high-quality machines can be a significant investment, consider the long-term savings and productivity gains they can provide. Assess the total cost of ownership, including maintenance and operational costs.
Conclusion
In today's competitive business environment, maximizing efficiency and minimizing costs are essential for success. Automatic label applicators represent a powerful solution that can revolutionize your labeling processes. By understanding their operation, benefits, and how to select the right model, businesses across various industries — whether in printing services, electronics, or computers — can leverage these machines to gain a competitive edge.
Investing in an automatic label applicator not only streamlines production but also enhances quality control and customer satisfaction. As you embark on this journey towards automation, ensure you explore the best options available to meet your unique business needs. For further assistance in navigating your options, visit omegabrand.com to discover top-of-the-line solutions tailored to your specifications.